Flexible return policies have made customers more comfortable shopping online as they reduce risks, fear, and uncertainties for the customer. This is beneficial for building customer loyalty and avoiding dissatisfaction among customers who may take their business elsewhere. However, returns are an expensive affair for businesses
According to market research agency Gitnux, e-commerce return rates are expected to reach $1.4 trillion by 2025. Additionally, businesses may incur expenses for the transportation of returned products. To address this challenge, companies need efficient reverse logistics processes to manage returns effectively and minimize costs.
In this blog post, we will explore the concept of reverse logistics and provide strategies for enhancing your company's reverse logistics process.
What Is Reverse Logistics?
Reverse logistics refers to managing the return of goods from customers to suppliers or manufacturers. This includes handling returns, recycling, and disposal of products. It starts from the end consumer and moves backward through the supply chain. Invesp reports that approximately 30% of online purchases are returned due to reasons like receiving incorrect, damaged, or misrepresented products.
An effective reverse logistics strategy aims to manage returned products efficiently, considering factors like reuse, recycling, or safe disposal. Besides affecting businesses, these returns pose significant environmental challenges, with an estimated EUR 6 billion worth of returned items ending up in landfills yearly. This shows how important it is for companies to improve their return processes and include them in their supply chain plan. Efficient reverse logistics is crucial for minimizing waste and maximizing value in the supply chain.
The Significance of Reverse Logistics for Your Business
Reverse logistics is key to maintaining a smooth flow of goods within a business. This process helps cut costs, add value, reduce risks, and effectively complete the product life cycle.
According to Gartner Research, approximately 70% of businesses are considering investments in the circular economy. This approach involves traditional logistics followed by a closed-loop supply chain, ensuring sustainability and efficiency.
The Circular Economy
Reverse logistics holds importance for businesses as it enhances customer satisfaction through efficient returns management, reduces waste and costs through recycling and reuse, and enhances brand reputation by showcasing environmental responsibility.
In this system, companies find alternative uses for discarded products through recovery, repair, and recycling, thus adding value to materials once deemed as waste. The circular economy ensures compliance with regulations requiring producers to adopt sustainable practices. These regulations offer incentives for waste prevention, research, development, and recycling while imposing penalties for unsustainable waste practices.
Value Creation through Reverse Logistics
Reverse logistics creates value by transforming waste into sales and fostering customer trust. Businesses resell, reuse, and recycle returned products, minimizing storage and distribution costs. Some studies state that less than half of returned goods are resold at full price, emphasizing the importance of finding optimal disposition options for returned items.
For instance, retail businesses like B-Stock resell returned goods, contributing to the company's profitability and sustainability goals. Whether businesses segregate their forward and reverse logistics or integrate them, they aim to maximize profitability and efficiency in supply chain activities. Companies adopt strategies tailored to their experiences, product values, and return volumes to benefit all stakeholders.
Challenges in Reverse Logistics
Creating a personalized plan for reverse logistics involves carefully tracking and studying your company's logistics activities over time. Assessing your supply chain setup is crucial to ensure it's ready to handle reverse logistics smoothly.
However, this task can be both time-consuming and challenging. Manual analysis of reverse logistics can lead to mistakes, especially for companies operating in different places, making it hard to plan return routes efficiently. Adjusting your reverse logistics plan to meet rising demands as your company grows can be tricky.
To address these issues, you might consider working with logistics partners like Tata BB Matrix or using software to automate and monitor your reverse logistics tasks.
Different Types of Reverse Logistics
There are various types of reverse logistics that businesses experience in their operations:
1. Product Returns
Customers may return products for various reasons, including damage during delivery, wrong size, defects, or dissatisfaction.
For instance, if a customer orders a pair of shoes online and finds them the wrong size upon arrival, they may initiate a return process. Similarly, if a consumer receives a damaged electronic device, they may request a replacement. Sometimes, products stop working within the warranty period, prompting customers to seek repairs or replacements.
2. Recalls
Recalls occur when companies need to withdraw defective products from the market to ensure consumer safety. For example, in December 2021, Tesla announced a recall of nearly 475,000 electric vehicles (EVs) worldwide due to a potential software issue affecting their backup camera systems. The recall addressed safety concerns related to compromised visibility while reversing, posing a risk of accidents.
According to Tesla's estimates, the recall was projected to cost the company approximately $332 million. This recall process involved:
- Identifying the affected vehicles.
- Notifying customers through various channels.
- Scheduling appointments for repairs at authorized service centers.
- Updating the software to resolve the issue.
Tesla prioritized customer safety and satisfaction throughout the recall process to maintain its reputation and adhere to regulatory requirements.
3. Repairs
Companies may offer repair services to customers when products are damaged or malfunctioning within the warranty period.
For instance, if a laptop develops a technical issue during the warranty period, the manufacturer may arrange for the device to be collected, repaired, and returned to the customer. Despite the costs and logistics involved, offering repair services can improve customer satisfaction and loyalty by demonstrating a commitment to quality and after-sales support.
4. Recycling
Reverse logistics can involve collecting recyclable waste from consumers to dispose of it responsibly.
For example, companies may implement take-back programs for used electronics or packaging materials. Coca-Cola's "World Without Waste" initiative aims to collect and recycle a bottle or can for each sold by 2030, reducing environmental impact. Additionally, some manufacturers collect empty product containers through reverse logistics to reuse them, minimizing waste and resource consumption.
5. Remanufacturing or Refurbishment
Reverse logistics may involve remanufacturing, refurbishing, or reconditioning products to extend their lifespan and minimize waste. These activities include repairing, rebuilding, and reworking products to make them suitable for resale or reuse.
Companies may recover interchangeable parts from other products through cannibalization to reduce costs and resources. Reconditioning typically involves disassembling, cleaning, and reassembling products to restore functionality and appearance.
6. Packaging Management
Packaging management in reverse logistics focuses on optimizing the reuse of packing materials to reduce waste and environmental impact. Companies may implement strategies to collect and reuse packaging materials, minimizing the need for new packaging and promoting sustainability in supply chain operations.
7. Failed Deliveries
Failed deliveries occur when customers are unavailable or refuse to accept packages upon delivery. In such cases, delivery drivers return the packages to the sorting center for investigation and resolution. Multiple failed deliveries can strain the reverse supply chain, increasing costs and operational inefficiencies. Implementing initiatives to minimize failed deliveries, such as improved customer communication or optimized delivery routes, is essential for efficient reverse logistics management.
8. End-of-Life (EOL)
Products that reach the end of their useful life or become obsolete are considered end-of-life (EOL). Manufacturers often face challenges managing EOL products, including disposal or recycling, to minimize environmental impact. EOL management strategies aim to handle obsolete products responsibly, recover valuable materials, and mitigate potential environmental risks associated with product disposal.
A technology company implements an EOL recycling program, allowing customers to return old electronic devices for responsible disposal and recycling, reducing electronic waste and environmental pollution.
Five Strategies for Enhancing Your Reverse Logistics Process
Handling returns efficiently is important for preserving brand reputation and customer loyalty. Here are five strategies for effective reverse logistics:
1. Conduct a Root Cause Analysis
To address the root causes of returns, businesses must analyze why customers are sending products back. This involves identifying potential issues with product usability, instructions, or quality. Companies can tailor their return policies and product offerings to reduce return rates by understanding the customer journey and gathering feedback.
2. Establish Transparent Monitoring Systems
Implementing monitoring systems throughout the reverse supply chain provides visibility into how returned products are handled. By tracking product movements and identifying areas for improvement, businesses can enhance product quality and optimize inventory management. This insight enables companies to make better decisions about repairing, replacing, or disposing of returned items.
3. Implement Clear Return Policies
Statista found that nearly 80% of online consumers are unlikely to buy from the same retailer again if they had a bad experience returning something. Clear and customer-friendly return policies are essential for reducing friction in the return process. By providing easy-to-understand guidelines and streamlining return procedures, companies can improve customer satisfaction and minimize the workload on customer service teams. Ensuring that both customers and employees are well-informed about return policies promotes efficiency and consistency.
Around 74% of consumers believe that US retailers must improve their returns process. It's essential to assess your business policies and make necessary changes. For example, consider offering specific time slots for convenience instead of providing broad pickup windows. This adjustment can reduce wait times for customers and enhance their overall experience.
4. Invest in Technology
Technology such as Warehouse Management Systems (WMS) and Transportation Management Systems (TMS) improves efficiency and accuracy in handling returns. These systems enable real-time tracking of returned products and facilitate seamless stakeholder communication.
Additionally, implementing VoIP phones enhances collaboration among remote teams, ensuring effective customer service and support. Consider integrating Tata BB Matrix into your operations for streamlined order management, automated warehouse processes, and enhanced quality control and compliance measures. Experience real-time order tracking and improved operational efficiency with our comprehensive solution.
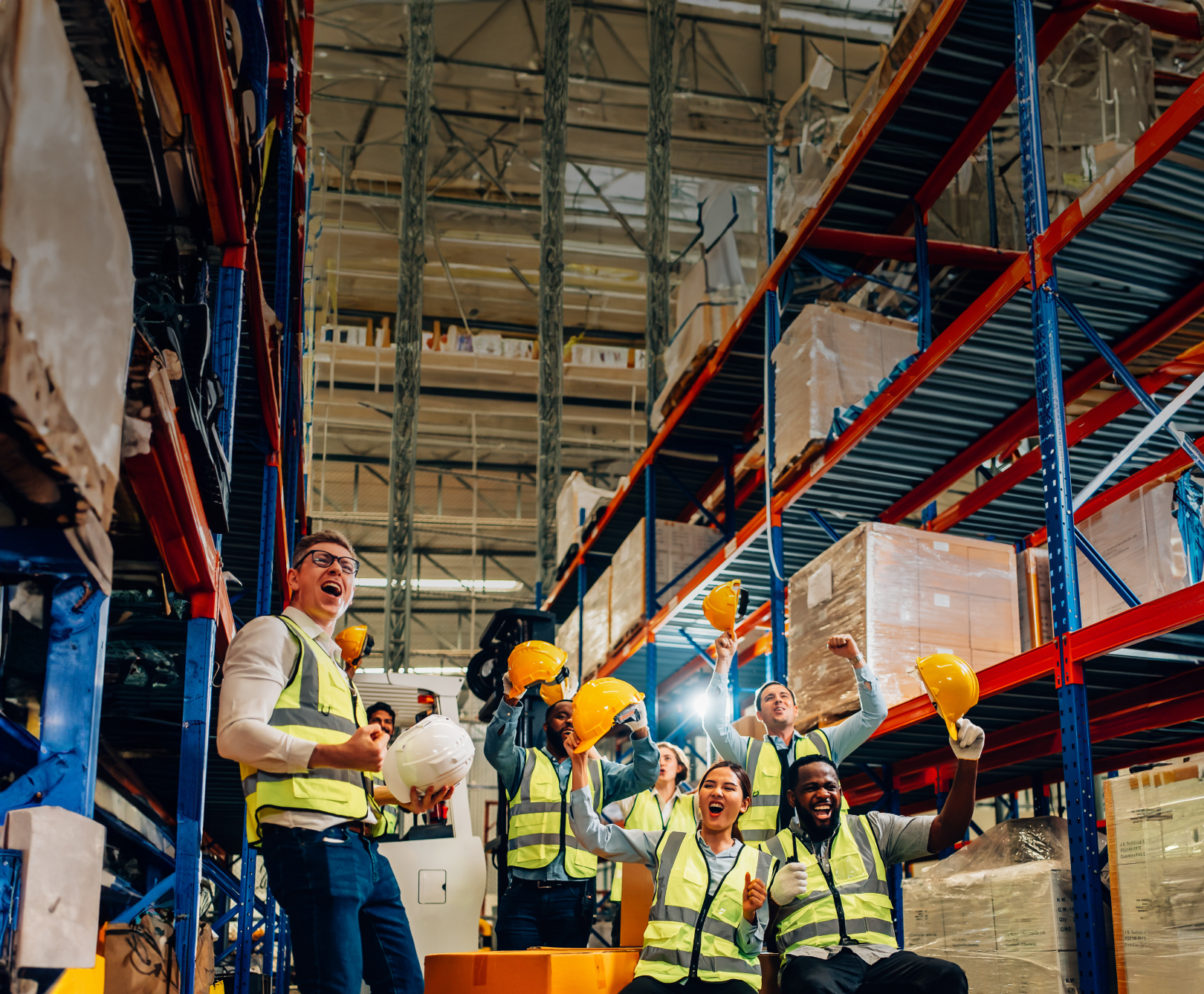
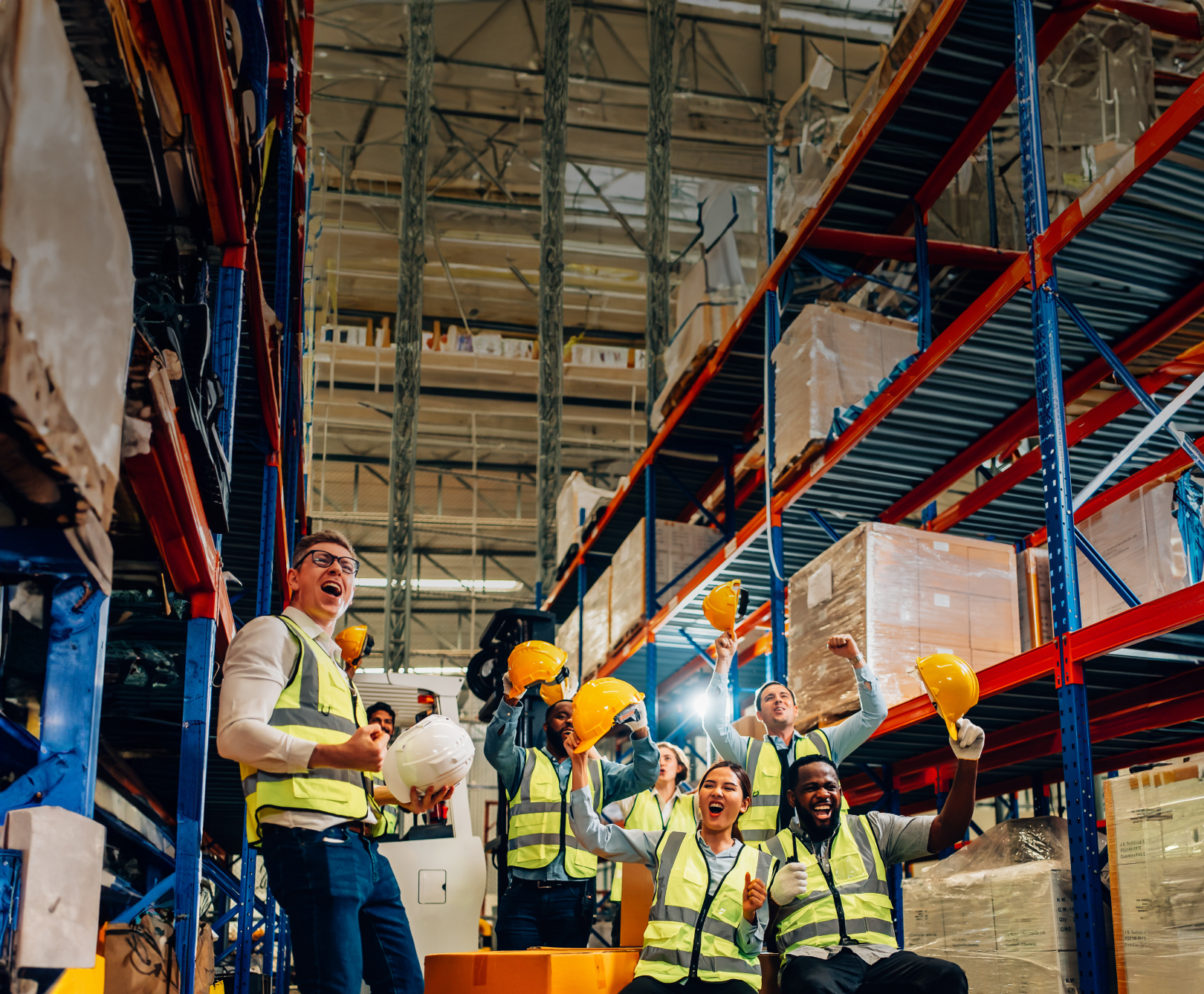
5. Simplify Return Labeling
Including return labels in the original packaging simplifies the return process for customers and retailers alike. By offering prepaid return labels and integrating them into invoices, businesses can expedite return shipments and improve overall process efficiency. This proactive approach reduces delays and enhances customer satisfaction, demonstrating a commitment to service excellence.
Ensuring Smooth Reverse Logistics Operations With Tata BB Matrix
Effectively managing reverse logistics is important for maintaining your business reputation, delivering quality customer service, and enhancing customer satisfaction.
Consider employing SaaS solutions like Tata BB Matrix to improve your reverse logistics process. Our software streamlines driver routes, informs customers about deliveries and pickups, and provides proof of delivery through automation.
Using the right software with omnichannel capabilities can optimize both forward and reverse logistics, enabling business expansion and better serving customers while reducing transportation expenses.
To learn more, book your free demo with us today!
FAQs
How can companies know if their return process is working well?
Businesses can measure the effectiveness of reverse logistics processes by tracking key performance indicators (KPIs) such as return rates, return processing times, product recovery rates, and customer satisfaction scores. By analyzing these metrics, companies can identify areas for improvement and optimize their reverse logistics operations.
What are some common misconceptions about reverse logistics, and how can they be addressed?
Common misconceptions about reverse logistics include viewing it solely as a cost center or assuming that returns are always negative for businesses. To address these misconceptions, companies can emphasize the value of efficient reverse logistics in enhancing customer satisfaction, minimizing waste, and recovering value from returned products.
How can businesses effectively manage returns from multiple sales channels and geographic locations?
Businesses can effectively manage returns from multiple sales channels and geographic locations by implementing centralized return processing systems, leveraging automated tracking and routing technology, and establishing clear communication channels with customers and partners. This ensures consistency and efficiency in managing returns across diverse channels and locations.
What role does data analytics play in optimizing reverse logistics processes?
Data analytics is crucial in optimizing reverse logistics processes by providing insights into return patterns, identifying root causes of returns, and predicting future return trends. By leveraging advanced analytics tools, businesses can make data-driven decisions to reduce costs, streamline processes, and improve customer satisfaction.
How can companies reduce the environmental effects of reverse logistics?
Businesses can minimize the environmental impact of reverse logistics operations by implementing sustainable practices such as product refurbishment, recycling, and eco-friendly packaging. Additionally, optimizing transportation routes and consolidating shipments can reduce carbon emissions associated with return transportation.
What are some emerging trends and technologies shaping the future of reverse logistics?
Emerging trends and tech shaping the future of reverse logistics include:
- The adoption of blockchain for transparent tracking.
- The use of AI for predictive analytics.
- The integration of IoT devices for real-time monitoring.
These innovations enable greater visibility, efficiency, and sustainability in reverse logistics operations.